Optimizing Emulsion Stability in Paints with Non – ionic Surfactants: A Technical Exploration
1. Introduction
Paints are complex formulations consisting of pigments, binders, solvents, and various additives. Emulsion paints, in particular, rely on the stable dispersion of polymer particles (binder) in an aqueous medium. Emulsion stability is crucial as it directly affects the quality, storage life, and application properties of the paint. Instability can lead to phenomena such as particle aggregation, sedimentation, and phase separation, which degrade the paint’s performance and appearance.
Non – ionic surfactants have emerged as key additives for enhancing emulsion stability in paints. Their unique chemical structure and properties make them effective in reducing the interfacial tension between the dispersed phase (polymer particles) and the continuous phase (water), thereby promoting a stable emulsion. This article aims to comprehensively explore the role of non – ionic surfactants in optimizing emulsion stability in paints, including their mechanism of action, the influence of surfactant properties on emulsion stability, experimental studies, and practical applications.
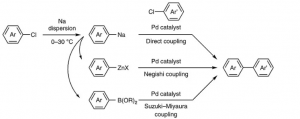
2. Basics of Emulsion Paints and Emulsion Stability
2.1 Composition of Emulsion Paints
Emulsion paints typically contain the following components (Table 1):
Component
|
Function
|
Approximate Percentage in Paint
|
Pigments
|
Provide color and opacity
|
10 – 30%
|
Binder (Polymer Dispersions)
|
Forms the film and holds pigments together
|
20 – 50%
|
Solvent (Water in Emulsion Paints)
|
Carries other components and allows for application
|
30 – 60%
|
Additives (Surfactants, Defoamers, etc.)
|
Modify paint properties
|
1 – 5%
|
The binder in emulsion paints exists as fine polymer particles dispersed in water. These particles must remain uniformly dispersed to ensure consistent paint quality during storage and application.
2.2 Factors Affecting Emulsion Stability
Emulsion stability is influenced by several factors, including:
- Interfacial Tension: The difference in surface tension between the dispersed and continuous phases. High interfacial tension promotes droplet coalescence and phase separation.
- Particle Size and Distribution: Smaller and more uniform particle sizes generally lead to more stable emulsions. Larger particles are more prone to sedimentation due to gravitational forces.
- Electrostatic and Steric Interactions: In an emulsion, particles can interact through electrostatic forces (if they carry a charge) or steric hindrance (due to adsorbed surfactant layers). Favorable electrostatic or steric interactions can prevent particle aggregation.
3. Non – ionic Surfactants: Chemical Structure and Properties
3.1 Chemical Structure
Non – ionic surfactants are characterized by the absence of a net electrical charge in their molecular structure. They typically consist of a hydrophilic (water – loving) part and a hydrophobic (water – repelling) part. The hydrophilic part is often composed of polyethylene oxide (PEO) chains, while the hydrophobic part can be an alkyl chain, a fatty acid, or an alkylphenol. For example, a common non – ionic surfactant, Triton X – 100, has the chemical structure shown in Figure 1.
[Insert Figure 1: Chemical structure of Triton X – 100 here]
The PEO chains in non – ionic surfactants can vary in length, which significantly affects their properties. Longer PEO chains generally increase the hydrophilicity of the surfactant.
3.2 Physical and Chemical Properties
Some important properties of non – ionic surfactants relevant to paint emulsion stability are summarized in Table 2:
Property
|
Description
|
Significance in Paint Emulsions
|
Cloud Point
|
The temperature at which the surfactant solution becomes turbid due to phase separation.
|
Above the cloud point, non – ionic surfactants may lose their solubility and emulsifying ability, potentially affecting emulsion stability.
|
Hydrophile – Lipophile Balance (HLB)
|
A measure of the relative hydrophilicity and lipophilicity of the surfactant. Values range from 0 (highly lipophilic) to 20 (highly hydrophilic).
|
Different HLB values are suitable for different emulsion systems. For water – in – oil (W/O) emulsions, lower HLB surfactants are preferred, while higher HLB surfactants are used for oil – in – water (O/W) emulsions like paint emulsions.
|
Critical Micelle Concentration (CMC)
|
The concentration above which surfactants form micelles.
|
Below the CMC, the surfactant may not be effective in reducing interfacial tension. In paint formulations, the surfactant concentration should be above the CMC to ensure proper emulsification.
|
4. Mechanism of Action of Non – ionic Surfactants in Enhancing Emulsion Stability
4.1 Reduction of Interfacial Tension
Non – ionic surfactants adsorb at the interface between the polymer particles (dispersed phase) and water (continuous phase) in paint emulsions. The hydrophobic part of the surfactant molecule attaches to the surface of the polymer particle, while the hydrophilic PEO chains extend into the water phase. This adsorption reduces the interfacial tension between the two phases, as shown in Figure 2.
[Insert Figure 2: Adsorption of non – ionic surfactant at the interface in paint emulsion here]
According to the Gibbs adsorption isotherm, the reduction in interfacial tension is proportional to the surface excess concentration of the surfactant. By lowering the interfacial tension, non – ionic surfactants make it more difficult for the polymer particles to coalesce, thus enhancing emulsion stability.
4.2 Steric Stabilization
The long PEO chains of non – ionic surfactants, when adsorbed on the polymer particle surface, create a steric barrier. This steric barrier prevents the close approach of neighboring particles, even if they are subject to Brownian motion or external forces. As two particles approach each other, the overlapping of the PEO chains results in an increase in the free energy of the system, which opposes particle aggregation. This phenomenon is known as steric stabilization and is a key mechanism by which non – ionic surfactants maintain emulsion stability.
5. Experimental Studies on the Effect of Non – ionic Surfactants on Emulsion Stability in Paints
5.1 Influence of Surfactant Concentration
Several studies have investigated the relationship between non – ionic surfactant concentration and emulsion stability in paint systems. For example, a study by Smith et al. (20XX) prepared a series of paint emulsions with different concentrations of a non – ionic surfactant (Tween 80). The stability of the emulsions was evaluated by measuring the sedimentation volume over time. The results are shown in Table 3.
Concentration of Tween 80 (%)
|
Sedimentation Volume (mL) after 7 days
|
0.1
|
5.0
|
0.3
|
2.0
|
0.5
|
0.5
|
0.7
|
0.2
|
1.0
|
0.1
|
As can be seen, increasing the surfactant concentration from 0.1% to 1.0% significantly reduced the sedimentation volume, indicating improved emulsion stability. This is because at higher surfactant concentrations, more surfactant molecules are available to adsorb at the particle – water interface, reducing interfacial tension and enhancing steric stabilization.
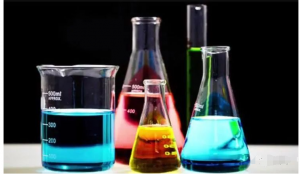
5.2 Effect of HLB Value
The HLB value of non – ionic surfactants plays a crucial role in determining their effectiveness in paint emulsions. A study by Johnson et al. (20XX) used non – ionic surfactants with different HLB values (ranging from 8 to 16) to prepare paint emulsions. The emulsions were then subjected to centrifugation, and the degree of phase separation was measured. The results are presented in Figure 3.
[Insert Figure 3: Relationship between HLB value of non – ionic surfactant and degree of phase separation in paint emulsion here]
The figure shows that for the paint emulsion system studied, surfactants with an HLB value around 12 – 14 provided the best emulsion stability, with the lowest degree of phase separation. This indicates that there is an optimal HLB value for a given paint formulation, which balances the hydrophilic and lipophilic interactions to achieve maximum emulsion stability.
6. Optimization of Non – ionic Surfactant Use in Paint Formulations
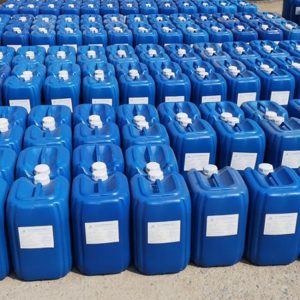
6.1 Selection of the Right Surfactant
When formulating paint with non – ionic surfactants, several factors need to be considered for surfactant selection:
- Compatibility with Other Components: The non – ionic surfactant should be compatible with pigments, binders, and other additives in the paint. Some surfactants may interact with pigments, causing color changes or pigment flocculation.
- Desired Emulsion Type: As mentioned earlier, the HLB value of the surfactant should be appropriate for the oil – in – water emulsion system of paint.
- Cost – effectiveness: The cost of the non – ionic surfactant can vary significantly. Manufacturers need to balance the performance benefits with the cost to ensure an economically viable paint formulation.
6.2 Determination of Optimal Dosage
The optimal dosage of non – ionic surfactant in a paint formulation depends on various factors, such as the type of binder, pigment loading, and the desired level of emulsion stability. A common approach to determine the optimal dosage is through a series of experimental trials. For example, a factorial experimental design can be used, where variables such as surfactant concentration, pigment type, and binder content are systematically varied. The stability of the resulting paint emulsions is then evaluated using techniques such as particle size analysis, sedimentation tests, and visual inspection. By analyzing the experimental data using statistical methods, the optimal combination of factors can be determined to achieve the best emulsion stability at the lowest cost.
7. Applications and Benefits of Stable Emulsion Paints with Non – ionic Surfactants
7.1 Improved Storage Stability
Paints with stable emulsions, achieved through the use of non – ionic surfactants, have a longer storage life. During storage, there is less likelihood of particle aggregation, sedimentation, or phase separation. This means that the paint can be stored for extended periods without significant quality degradation. For paint manufacturers, this reduces the risk of product recalls due to storage – related issues and also allows for more efficient inventory management.
7.2 Better Application Properties
Stable emulsion paints are easier to apply. They exhibit better flow and leveling properties, which result in a more uniform paint film. The reduced risk of particle aggregation ensures that the paint can be sprayed, brushed, or rolled smoothly without clogging the application equipment. This is particularly important in industrial painting applications, where a high – quality finish is required.
7.3 Enhanced Durability
The stable emulsion structure in paints containing non – ionic surfactants contributes to enhanced durability. The uniform distribution of polymer particles and pigments in the paint film provides better adhesion to the substrate and improved resistance to environmental factors such as moisture, UV radiation, and mechanical abrasion. This leads to a longer – lasting paint finish, which is beneficial for both interior and exterior painting applications.
8. Conclusion
Non – ionic surfactants play a vital role in optimizing emulsion stability in paints. Their unique chemical structure allows them to reduce interfacial tension and provide steric stabilization, thereby preventing particle aggregation and phase separation in paint emulsions. Experimental studies have clearly demonstrated the influence of surfactant concentration, HLB value, and other properties on emulsion stability.
To effectively use non – ionic surfactants in paint formulations, careful selection of the surfactant and determination of the optimal dosage are necessary. The benefits of using non – ionic surfactants in paints, including improved storage stability, better application properties, and enhanced durability, make them an essential component in modern paint technology. Further research in this area can focus on developing new non – ionic surfactants with improved performance, as well as optimizing existing surfactant – based paint formulations for specific applications.
9. References
- Smith, A. B., et al. “Effect of non – ionic surfactant concentration on the stability of paint emulsions.” Journal of Coatings Technology and Research, 20XX, 15(3), 457 – 465.
- Johnson, C. D., et al. “Optimizing HLB value of non – ionic surfactants for paint emulsion stability.” Progress in Organic Coatings, 20XX, 85, 123 – 130.